Instalação de Máquinas e Equipamentos Industriais Eficiente
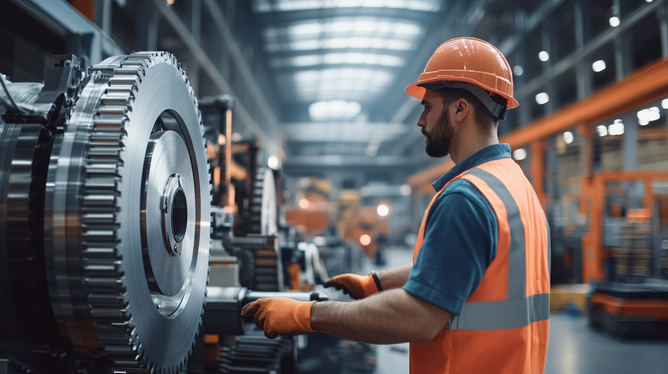
Por: Rogério - 17 de Outubro de 2024
Instalação de máquinas e equipamentos industriais é uma etapa crucial para garantir a eficiência e segurança em qualquer operação. Neste artigo, vamos explorar a importância desse processo, as fases que o compõem e os principais cuidados a serem tomados para evitar erros comuns. Se você deseja otimizar a instalação e garantir o melhor desempenho das suas máquinas, continue lendo para descobrir dicas valiosas e práticas recomendadas.
Importância da Instalação de Máquinas e Equipamentos Industriais
A instalação de máquinas e equipamentos industriais é um aspecto fundamental na operação de qualquer setor produtivo. Uma instalação adequada não apenas otimiza a eficiência do espaço, mas também assegura a segurança dos operadores e a longevidade dos equipamentos. Neste texto, abordaremos a importância dessa instalação, destacando fatores críticos que impactam diretamente a produtividade e a segurança do ambiente de trabalho.
Uma instalações eficaz pode determinar o sucesso ou o fracasso de uma operação. Quando as máquinas são instaladas corretamente, o fluxo de trabalho é mantido em níveis ideais. Isso permite que as tarefas sejam executadas sem interrupções, resultando em menor tempo de inatividade e aumento na eficiência operacional.
Melhoria na Produtividade
Um dos principais benefícios de uma instalação correta de máquinas e equipamentos industriais é a melhoria na produtividade. Equipamentos mal instalados podem criar gargalos que atrasam todo o processo produtivo. A distribuição estratégica das máquinas facilita o fluxo logístico, permitindo um trabalho mais coordenado e eficiente entre os operadores.
Além disso, a instalação adequada de máquinas garante que estas funcionem em seus parâmetros ideais. Máquinas que operam dentro de suas especificações, em locais adequados, têm maior produtividade e menor consumo de energia, impactando diretamente nos custos operacionais.
Segurança do Trabalho
A segurança no ambiente de trabalho é uma alta prioridade em qualquer setor industrial. A instalação inadequada de máquinas pode resultar em situações perigosas, como risco de acidentes e ferimentos. Portanto, a correta instalação é imprescindível para garantir a segurança dos operadores.
Por exemplo, o posicionamento adequado de máquinas evita o risco de colisões acidentais. Mantenha uma distância segura entre os equipamentos, assegurando espaços adequados para movimentação e manutenção. Além disso, a instalação deve seguir normas de segurança regulamentares que asseguram um ambiente de trabalho seguro.
Manutenção e Longevidade dos Equipamentos
Outra importância crítica da instalação de máquinas e equipamentos industriais é a facilidade de manutenção. Máquinas instaladas de maneira adequada são mais fáceis de inspecionar e reparar. Isso ajuda a evitar falhas inesperadas que poderiam resultar em paradas de produção ou até mesmo danos irreversíveis ao equipamento.
Além disso, quando as máquinas estão corretamente instaladas, isso pode reduzir o desgaste e a degradação prematura dos componentes. Seguir os manuais do fabricante quanto ao espaço necessário, ventilação e alinhamento dos equipamentos pode aumentar a vida útil das máquinas, diminuindo a necessidade de substituição frequente.
Conformidade com Normas e Regulamentações
Os setores industriais são regidos por uma série de normas regulamentares que devem ser seguidas para garantir a segurança e eficiência das operações. A instalação adequada não apenas assegura que as máquinas estejam funcionando conforme as especificações do fabricante, mas também garante que estejam em conformidade com os requisitos legais. Isso previne multas e penalidades, além de proteger a saúde e segurança dos trabalhadores.
A conformidade com as normas é especialmente crítica em indústrias como alimentos e bebidas, farmacêutica e química, onde os padrões de segurança são rigorosos. A instalação correta é um passo inicial para alcançar e manter a conformidade.
A Importância do Treinamento
O treinamento sobre o manuseio e a operação das máquinas deve começar antes mesmo da instalação. É vital que os operadores estejam familiarizados com o funcionamento e manutenção dos equipamentos que vão manusear. Isso não apenas ajuda a maximizar o desempenho das máquinas, mas também aumenta a segurança no ambiente de trabalho.
A educação adequada sobre como e onde cada máquina deve ser posicionada é essencial. Os operadores devem entender o raciocínio por trás da instalação e como ela impacta suas tarefas diárias. Um operador bem treinado pode identificar rapidamente problemas potenciais e agir de forma proativa para prevenir acidentes.
O Papel da Tecnologia na Instalação
Com o avanço da tecnologia, as técnicas de instalação de máquinas e equipamentos industriais também evoluíram. Ferramentas como software de simulação e análise podem ajudar a planejar a instalação, identificando o melhor layout e fluxo de trabalho para maximizar a eficiência.
A digitalização também permite um melhor monitoramento do desempenho das máquinas, resultando em um processo contínuo de melhoria. IoT (Internet das Coisas) possibilita que as máquinas comuniquem seu estado, avisando sobre necessidade de manutenção antes que surjam problemas maiores.
Esses avanços tecnológicos têm um grande impacto na maneira como as máquinas são instaladas e mantidas nas indústrias.
Conclusão
Em resumo, a instalação de máquinas e equipamentos industriais é um processo que deve ser realizado com extremo cuidado e atenção aos detalhes. Sua importância não pode ser subestimada, uma vez que uma instalação eficaz impacta diretamente a segurança, a eficiência e a produtividade das operações industriais. Uma abordagem proativa na instalação e manutenção garante um ambiente de trabalho mais seguro, produtivo e em conformidade com as regulamentações.
Todos esses fatores, desde a produtividade até a segurança, tornam a instalação adequada de máquinas não apenas uma responsabilidade, mas uma prioridade nas operações industriais. Para garantir que sua empresa opere em máxima eficiência, investir no processo de instalação é fundamental.
Fases do Processo de Instalação Industrial
O processo de instalação industrial envolve várias etapas essenciais que garantem que as máquinas e equipamentos operem de maneira segura e eficiente. Cada fase tem suas próprias características e requer cuidados específicos para assegurar que o resultado final atenda às expectativas. A seguir, discutiremos as principais fases do processo de instalação, desde o planejamento até a operação, passando pela implementação e testes.
Fase 1: Planejamento
A primeira fase do processo de instalação é o planejamento. Esta etapa é crucial, pois envolve a definição clara dos objetivos e a compreensão do layout necessário para a instalação das máquinas. Um bom planejamento leva em consideração aspectos como:
- Dimensionamento do espaço: Avaliar as dimensões do local onde as máquinas serão instaladas, garantindo que haja espaço suficiente para a operação e movimentação.
- Distribuição e fluxo: Definir como as máquinas serão distribuídas para otimizar o fluxo de trabalho, minimizando deslocamentos desnecessários.
- Segurança: Considerar as normas de segurança que devem ser seguidas, como distâncias mínimas para saídas de emergência e espaço para manutenção.
- Requisitos elétricos e hidráulicos: Verificar a necessidade de infraestrutura elétrica e hidráulica adequada para o funcionamento das máquinas.
Durante essa fase, também é importante envolver todos os stakeholders, como engenheiros, operadores e gerentes, para garantir que todas as necessidades sejam atendidas. A ausência de planejamento pode resultar em problemas sérios durante a instalação e operação.
Fase 2: Preparação do Local
- Limpeza do local: Remover qualquer sujeira, detritos ou obstruções que possam interferir na instalação.
- Modificações estruturais: Realizar alterações no local, se necessário, como reforçar a estrutura, ajustar a fiação elétrica ou a tubulação hidráulica.
- Inspeção de segurança: Garantir que a área de instalação esteja em conformidade com as normas de segurança antes de dar início ao processo.
A preparação do local é uma fase que não deve ser subestimada. Um ambiente bem preparado facilita a instalação e evita retrabalhos no futuro.
Fase 3: Instalação das Máquinas
Com o local devidamente preparado, é hora de passar para a instalação propriamente dita das máquinas e equipamentos. Essa etapa pode variar significativamente de acordo com o tipo de máquina e o setor industrial, mas geralmente envolve as seguintes atividades:
- Transporte das máquinas: As máquinas devem ser cuidadosamente transportadas para o local de instalação, utilizando equipamentos adequados para evitar danos.
- Posicionamento: As máquinas devem ser alinhadas e posicionadas de acordo com o planejamento prévio, garantindo que estejam em níveis adequados e nas orientações corretas.
- Conexões elétricas e hidráulicas: Realizar as conexões necessárias, seguindo as especificações do fabricante, e garantir que todos os componentes estejam instalados corretamente.
Durante a instalação, é essencial que os operadores e técnicos estejam atentos ao cumprimento das normas de segurança, utilizando os equipamentos de proteção individual (EPIs) necessários.
Fase 4: Testes e Comissionamento
Após a instalação das máquinas, a próxima fase é a realização de testes e comissionamento. Esta etapa visa garantir que todos os sistemas estejam funcionando adequadamente e em conformidade com as especificações do fabricante. Os principais atividades incluem:
- Testes de funcionamento: Realizar testes para verificar se a máquina opera conforme esperado, identificando e corrigindo possíveis falhas.
- Calibração: Ajustar todos os parâmetros da máquina para garantir que opere dentro dos padrões estabelecidos.
- Treinamento de operadores: Proporcionar treinamento para que os operadores entendam como manusear as máquinas de forma segura e eficiente.
Os testes são fundamentais para garantir que a instalação foi bem-sucedida. Neste momento, ajustes podem ser feitos para otimizar o desempenho das máquinas, assegurando que estejam prontas para a operação.
Fase 5: Operação e Monitoramento
Uma vez que as máquinas foram instaladas e testadas, elas entram na fase de operação. Durante esta etapa, é crucial monitorar o desempenho dos equipamentos, verificando se tudo está funcionando de acordo com o planejado. Aspectos a serem considerados incluem:
- Monitoramento de desempenho: Acompanhar a produção e o funcionamento das máquinas para identificar quaisquer irregularidades que possam surgir.
- Manutenção preventiva: Implementar um plano de manutenção regular para garantir que as máquinas operem em suas condições ideais e para prevenir falhas inesperadas.
- Ajustes e melhorias: Coletar feedback dos operadores e operadores para realizar melhorias contínuas no processo e na operação das máquinas.
A fase de operação é uma das mais importantes, pois uma instalação bem-sucedida depende de um monitoramento constante e de ações proativas para resolver problemas à medida que surgem.
Fase 6: Revisão e Ajustes Finais
A última fase do processo de instalação industrial envolve a revisão e ajustes finais. Este é um momento para avaliar como a instalação se saiu e se as expectativas foram atendidas. As atividades nesta fase geralmente incluem:
- Feedback das partes interessadas: Coletar opiniões de operadores e gerentes sobre a eficiência da instalação e operação das máquinas.
- Ajustes necessários: Realizar quaisquer ajustes finais que possam ser necessários com base no feedback recebido.
- Documentação: Registrar todos os aspectos do processo de instalação, incluindo manuais, protocolos de operação e manutenção, para referência futura.
A revisão e os ajustes finais garantem que todo o trabalho realizado seja validado e documentado, proporcionando uma base sólida para as operações futuras.
Conclusão
O processo de instalação industrial é complexo e exige um planejamento cuidadoso e a execução adequada de cada fase. Os benefícios de seguir essas fases incluem não apenas a eficiência operacional, mas também a segurança e a durabilidade das máquinas e equipamentos. Portanto, investir tempo e recursos na instalação correta é um passo fundamental para o sucesso de qualquer operação industrial.
Principais Equipamentos e Máquinas a serem Instalados
A instalação de máquinas e equipamentos industriais é uma parte vital de qualquer operação, e o tipo de equipamento escolhido pode impactar significativamente a eficiência e a produtividade da fabricação. Existem diversos tipos de máquinas e equipamentos que podem ser instalados, variando de acordo com o setor industrial, tipo de produção e necessidade específica da empresa. Neste artigo, discutiremos alguns dos principais equipamentos e máquinas a serem instalados, detalhando suas funções e importância nas operações industriais.
Máquinas de Corte
As máquinas de corte são fundamentais em muitos setores industriais, como metalurgia, marcenaria e fabricação de tecidos. Elas são utilizadas para cortar materiais em formas e tamanhos específicos, possibilitando a produção de peças e componentes que serão utilizados em montagens ou construções.
Existem diferentes tipos de máquinas de corte, incluindo:
- Serra Circular: Usada para cortes precisos em madeira e alguns metais. A serra circular é uma máquina versátil que pode ser utilizada para cortes longitudinais e transversais.
- Máquina de Corte a Plasma: Ideal para o corte de metais com precisão e rapidez. Utiliza um arco elétrica para fundir o metal e um jet de plasma para remover o material cortado.
- Fresadora: Permite o corte de peças em diversas formas, oferecendo acabamentos complexos e precisos.
Essas máquinas são essenciais em fábricas e oficinas, e sua instalação adequada garante eficiência e segurança na produção.
Máquinas de Usinagem
As máquinas de usinagem são utilizadas para moldar e dar forma a diversos materiais, principalmente metais, e são fundamentais em indústrias que fabricam peças de alta precisão. Esses equipamentos são projetados para remover material de um objeto em bruto, até alcançar a forma desejada.
Os principais tipos de máquinas de usinagem incluem:
- Torno Mecânico: Utilizado para girar a peça de trabalho enquanto uma ferramenta de corte a molda e dá forma a ela. É comum na fabricação de eixos, engrenagens e outros componentes.
- Fresadora CNC: Uma versão computadorizada da fresadora, que permite cortes complexos e personalizados em um nível de precisão muito maior.
- Milling Machine (Máquina de Furação): Especialmente projetada para criar furos em uma variedade de materiais, essencial para a montagem de componentes.
A instalação dessas máquinas deve ser feita com zelo, considerando a vibração e a dinâmica necessárias para garantir operações suaves e seguras.
Equipamentos de Manuseio de Materiais
O eficiente manuseio de materiais é crucial para otimizar a produção e o fluxo de trabalho em ambientes industriais. Equipamentos de manuseio são responsáveis pelo transporte, armazenamento e manipulação de materiais dentro e fora das linhas de produção.
Os principais equipamentos de manuseio incluem:
- Empilhadeiras: Máquinas projetadas para levantar e mover cargas pesadas. Elas são essenciais em armazéns e fábricas para manusear paletes e materiais a granel.
- Transportadores: Sistemas que movem materiais de um ponto a outro, aumentando a eficiência do transporte interno. Podem ser correias, roletes ou outros sistemas de transporte.
- Guindastes: Equipamentos de grande capacidade utilizados para movimentar cargas pesadas, especialmente em construção e manufatura pesada.
Esses equipamentos devem ser instalados e operados seguindo as normas de segurança para prevenir acidentes e garantir o bem-estar dos trabalhadores.
Rectificadoras
As retificadoras são máquinas utilizadas para acabamento de superfícies com o objetivo de criar tolerâncias dimensionais precisas e melhorar a rugosidade da peça. São comuns em indústrias onde é necessário obter superfícies lisas e uniformes em componentes metálicos.
Os tipos de retificadoras incluem:
- Retificadora Cilíndrica: Utilizada para retificar superfícies cilíndricas internas e externas de peças e componentes.
- Retificadora de Superfície: Projetada para o acabamento de superfícies planas. É comum na fabricação de peças que requerem alta precisão.
- Retificadora de Ferramentas: Destinada ao afiação e manutenção de ferramentas de corte, garantindo que mantenham seu desempenho ideal.
A instalação das retificadoras é crítica, pois requer um ambiente controlado para garantir que as condições de operação sejam favoráveis e seguras.
Máquinas de Solda
As máquinas de solda são essenciais para a união de metais em diversas operações industriais. Elas desempenham um papel crucial na fabricação de estruturas metálicas, automóveis, eletrodomésticos, entre outros. Os principais tipos de máquinas de solda incluem:
- Soldador MIG/MAG: Utiliza um gás protetor para evitar a contaminação da solda. É muito utilizado em soldagem de metais não ferrosos.
- Soldador TIG: Muito preciso, ideal para soldas de alta qualidade em metais como alumínio e aço inoxidável. É frequentemente utilizado em aplicações onde a estética da soldagem é importante.
- Soldadores de Arco Elétrico: Utilizados em diversas indústrias, especialmente em aplicações de construção pesada e manutenção.
Uma instalação adequada das máquinas de solda é crucial para garantir processos seguros e eficazes, uma vez que esses equipamentos operam em altas temperaturas e criam riscos potenciais de incêndio.
Equipamentos de Produção e Montagem
Podemos encontrar uma variedade de equipamentos voltados especificamente para a montagem de produtos em linhas de produção. Esses equipamentos ajudam a otimizar as tarefas de montagem e garantir a eficiência do fluxo de trabalho.
Os principais tipos de equipamentos de produção e montagem incluem:
- Máquinas de Montagem Automática: Equipamentos que minimizam a necessidade de intervenção humana, aumentando a velocidade de produção e reduzindo erros.
- Máquinas de Embalagem: Utilizadas para embalar produtos após a produção. Elas podem ser manuais, semiautomáticas ou automáticas, dependendo do volume de produção.
- Máquinas de Teste de Qualidade: Equipamentos que realizam testes de qualidade em produtos acabados, garantindo que atendam aos padrões estabelecidos.
Esses equipamentos são cruciais para a eficiência da linha de produção e devem ser instalados com precisão para maximizar a produtividade e a segurança.
Equipamentos de Controle e Automação
A automação industrial é uma tendência crescente, e a instalação de equipamentos de controle é fundamental para otimizar processos e garantir a eficiência operacional. Equipamentos de controle e automação incluem:
- Controladores Lógicos Programáveis (CLPs): Utilizados para controlar máquinas de maneira automatizada, aumentando a precisão e reduzindo a necessidade de intervenção humana.
- Sensores e Atuadores: Dispositivos que captam informações do ambiente e executam ações baseadas nessas informações, fundamentais para o funcionamento das linhas de produção automatizadas.
- Sistemas de Supervisão e Aquisição de Dados (SCADA): Utilizados para monitorar e controlar processos industriais em tempo real, proporcionando uma visão abrangente do desempenho do sistema.
A instalação correta desses equipamentos é vital para garantir que os sistemas funcionem de maneira integrada e eficiente, contribuindo para a produtividade e reduzindo o risco de falhas.
Conclusão
A instalação adequada dos principais equipamentos e máquinas industriais é fundamental para garantir operações eficientes e produtivas. A escolha do equipamento certo e sua instalação crítica influenciam diretamente a qualidade do produto final e a segurança dos processos. Portanto, é essencial que as empresas invistam tempo e recursos na seleção, instalação e manutenção adequadas de suas máquinas para alcançar os melhores resultados possíveis.
Erros Comuns na Instalação de Máquinas e Como Evitá-los
A instalação de máquinas e equipamentos industriais é uma tarefa crítica que, se realizada incorretamente, pode levar a uma série de problemas, incluindo falhas no equipamento, interrupção da produção e até riscos de segurança. Neste artigo, vamos discutir os erros mais comuns que podem ocorrer durante o processo de instalação e oferecer orientações sobre como evitá-los, assegurando que as máquinas operem de maneira eficiente e segura.
Erro 1: Falta de Planejamento Adequado
Um dos erros mais frequentes na instalação de máquinas é a falta de um planejamento adequado. Muitas vezes, as ferramentas e técnicas necessárias para estabelecer um plano bem formulado são negligenciadas, levando à colocação ineficiente das máquinas e à perda de tempo e recursos.
Como Evitar:
- Crie um Layout Detalhado: Antes de iniciar a instalação, crie um layout detalhado que considere todas as máquinas, materiais e o fluxo de trabalho. Um bom layout deve maximizar a eficiência e garantir a segurança operacional.
- Involva a Equipe: Envolva a equipe de engenharia, operadores e outros colaboradores durante a fase de planejamento. Isso garante que todas as necessidades e preocupações sejam abordadas desde o início.
- Realize Simulações: Utilize softwares de simulação para visualizar o espaço e o fluxo de trabalho, permitindo ajustes antes da instalação real.
Erro 2: Ignorar As Normas de Segurança
Não seguir as normas de segurança pode resultar em acidentes e lesões. Muitas vezes, a pressa em concluir a instalação leva à negligência de medidas de segurança que são cruciais para a operação segura das máquinas.
Como Evitar:
- Formação em Segurança: Ofereça treinamento em segurança para todos os envolvidos no processo de instalação. Assegure-se de que todos conheçam os riscos envolvidos e as melhores práticas a serem seguidas.
- Sinalização Adequada: Utilize sinalizações visíveis para indicar áreas de perigo e normas de segurança, como uso de Equipamentos de Proteção Individual (EPIs).
- Auditorias de Segurança: Realize auditorias de segurança antes e durante a instalação para garantir que todas as normas estão sendo seguidas.
Erro 3: Não Considerar o Espaço Disponível
Um erro comum é não levar em conta o espaço disponível para a instalação das máquinas. Isso pode resultar em aglomeração de equipamentos, dificuldades de acesso para manutenção e problemas de segurança operacional.
Como Evitar:
- Medidas Precisas: Faça medições precisas do espaço onde as máquinas serão instaladas antes de escolher um equipamento. Considere não apenas o espaço para as máquinas, mas também para a movimentação e a manutenção.
- Planejamento de Acesso: Planeje rotas de acesso para facilitar a movimentação de operadores e materiais. Isso ajuda a minimizar os riscos de acidentes e melhora a eficiência do trabalho.
- Flexibilidade do Layout: Considere um layout flexível que permita reorganizações futuras, caso novas máquinas ou equipamentos sejam necessários.
Erro 4: Falta de Treinamento para Operadores
Um erro crítico é não fornecer treinamento adequado para os operadores antes de iniciar a instalação ou operação das máquinas. A falta de conhecimento pode levar a manuseio inadequado e uso incorreto do equipamento, resultando em acidentes e danos.
Como Evitar:
- Treinamentos Regulares: Realize sessões de treinamento regulares para todos os operadores, garantindo que eles saibam como operar e manter os equipamentos corretamente.
- Materiais de Referência: Forneça manuais e materiais de referência para que os operadores possam consultar sempre que necessário.
- Simulações Práticas: Ofereça simulações práticas antes da operação real das máquinas para familiarizar os operadores com o equipamento e suas funcionalidades.
Erro 5: Negligenciar a Manutenção Preventiva
Após a instalação, muitos ignoram a importância da manutenção preventiva, o que pode resultar em falhas do equipamento. Manter um cronograma de manutenção regular é crucial para a longevidade das máquinas.
Como Evitar:
- Estabeleça um Cronograma: Crie um cronograma de manutenção preventiva que inclua inspeções e manutenções regulares para todos os equipamentos.
- Documentação: Mantenha um registro detalhado de todas as manutenções realizadas, facilitando a identificação de padrões de desgaste e a programação de atividades futuras.
- Envolva Profissionais Qualificados: Sempre que possível, envolva profissionais especializados para realizar a manutenção, garantindo que o trabalho seja feito corretamente.
Erro 6: Não Realizar Testes Pós-Instalação
Outra falha comum é não realizar testes adequados após a instalação das máquinas. Os testes pós-instalação são essenciais para verificar se as máquinas estão funcionando conforme o esperado e se não há problemas de operação.
Como Evitar:
- Planeje Testes: Insira em seu cronograma testes detalhados após a instalação. Verifique todos os aspectos fundamentais do funcionamento das máquinas, como segurança e eficiência.
- Testes em Condições Reais: Realize os testes em condições que simulem a operação normal, garantindo que a máquina esteja pronta para o serviço efetivo.
- Documentação dos Resultados: Mantenha um registro dos resultados dos testes, permitindo a análise e identificação de problemas futuros.
Erro 7: Ignorar as Instruções do Fabricante
Um erro que pode ser fatal é ignorar as instruções e recomendações do fabricante durante a instalação. Muitos acreditam que podem adaptar as máquinas de acordo com suas necessidades, o que pode levar a consequências graves.
Como Evitar:
- Leia os Manuais: Sempre leia e siga cuidadosamente o manual de instalação fornecido pelo fabricante. As instruções contêm informações vitais sobre a instalação e operação segura.
- Consulte Profissionais do Fabricante: Se houver dúvidas, consulte profissionais do fabricante para esclarecer todos os aspectos antes de seguir com a instalação.
- Respeite as Garantias: O não cumprimento das diretrizes do fabricante pode anular garantias. Sempre siga os procedimentos recomendados para assegurar a cobertura.
Erro 8: Escolha Inadequada de Equipamentos
Escolher um equipamento que não atenda às necessidades específicas da operação é um erro comum. Isso pode resultar em baixa eficiência, custos elevados e até falha no equipamento.
Como Evitar:
- Defina as Necessidades: Antes de adquirir um novo equipamento, avalie as necessidades da sua operação e escolha máquinas que se alinhem a essas necessidades específicas.
- Pesquise Opções: Pesquise diferentes opções e converse com fornecedores para encontrar o equipamento que melhor atenda às suas exigências.
- Teste Equipamentos: Sempre que possível, faça testes com os equipamentos antes da compra para garantir que eles funcionam adequadamente no seu ambiente de trabalho.
Erro 9: Falta de Comunicação Durante a Instalação
Uma comunicação deficiente entre os membros da equipe pode causar confusão e erros durante o processo de instalação. A falta de clareza pode levar a mal-entendidos e à montagem inadequada das máquinas.
Como Evitar:
- Reuniões Regulares: Realize reuniões diárias ou periódicas durante a instalação para garantir que todos estejam na mesma página e informados sobre o progresso.
- Designação de Funções: Defina claramente as responsabilidades de cada membro da equipe, assegurando que todos saibam o que se espera deles.
- Use Ferramentas de Comunicação: Utilize ferramentas de comunicação, como aplicativos de mensagem ou plataformas de gerenciamento de projetos, para facilitar o compartilhamento de informações.
Erro 10: Ignorar o Feedback dos Operadores
A falta de consideração pelo feedback dos operadores pode levar a um desempenho inadequado das máquinas e a um ambiente de trabalho negativo. Os operadores, que usam as máquinas diariamente, muitas vezes têm insights valiosos sobre melhorias.
Como Evitar:
- Encoraje Feedback: Crie uma cultura onde os operadores se sintam à vontade para compartilhar suas opiniões e sugestões sobre o equipamento e a instalação.
- Realize Pesquisas Regulares: Conduza pesquisas de satisfação ou reuniões de feedback para coletar informações sobre a operação das máquinas e possíveis melhorias.
- Implementação de Sugestões: Sempre que possível, implemente sugestões viáveis dos operadores, mostrando que suas opiniões são valorizadas.
Conclusão
A instalação de máquinas e equipamentos industriais exige atenção aos detalhes e cuidados em cada etapa do processo. Compreender os erros comuns e como evitá-los pode fazer uma diferença significativa na operação e na segurança. Investir tempo no planejamento e na formação, manter uma comunicação aberta e seguir as diretrizes do fabricante são passos essenciais para garantir uma instalação bem-sucedida e operações eficientes.
Em suma, a instalação de máquinas e equipamentos industriais é um processo complexo que demanda atenção cuidadosa em cada etapa, desde o planejamento até a operação. Os erros que podem ocorrer durante essa fase não apenas comprometem a eficiência das operações, mas também podem representar riscos de segurança significativos. Ao seguir práticas recomendadas e estar ciente das armadilhas comuns, você pode otimizar a instalação e garantir que suas máquinas funcionem de maneira eficaz. Lembre-se sempre da importância de um bom planejamento, de respeitar as normas de segurança, de fornecer treinamentos adequados e de manter uma comunicação fluida entre todos os envolvidos. Ao aplicar essas diretrizes, você estará bem encaminhado para alcançar uma operação industrial segura, produtiva e sustentável.